Kennerton Audio. About headphones, manufacturing culture and future plans
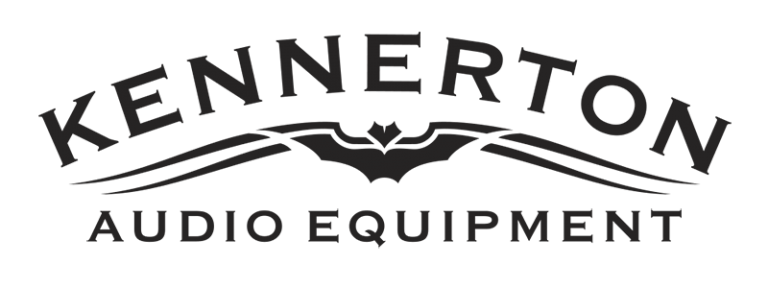
Kennerton Wodan headphones impressed me oh so much, so I immediately got myself invited to the Kennerton office. And asked them about different things. About everything I wanted.
Q: Let’s start with the current line of headphones. Why does this line look exactly this way and not in any other? How are these headphones models different from each other, what is your vision?
K: There are 9 models making the basis of the current line. These are Thror, Thekk, Tridi, Wodan and Odin (2019) for planars, Vali, Gjallarhorn, Magni and M12s (2020) for dynamic ones.
All planar models are open-back.
Let’s start with Thror headphones. Thror are the flagship of the line. These are the most smooth, balanced headphones of the line, the most ‘right’ from the common audiophile point of view, and extremely close to the Harman Target Response Curve in what’s related to the settings matter. We’ve put a lot of effort and time (and a significant budget, too) into their development. They reflect our vision of the ‘right’ sound, our progress relative to the previous flagship model, which is Odin (2015). The original Odin were very popular, but not everyone liked them. So while developing Thror, we tried to improve every weak point.
The next model is Thekk. Initially, Thekk were meant to become professional benchmark headphones with a new headband design, but then we started to experiment with sound — just a little quirks here and there. And that’s where we achieved a more individual sound delivery. We showed Thekk off at an exhibition and received a whole lot of ‘Spare us Thror, give us Thekk’ type of feedback. The model’s become especially popular among portable devices fans despite their open-back design. Long story short, it’s now the most popular model in Russia (after the Magni model). Thekk’s sound can be described as dark and thick.
As for the Thridi – they provide lighter sound delivery compared to Thror, and especially to Thekk. Thridi are also somewhat more flexible in terms of control and more agile compared to Thror, but at the same time, Thror still sound smoother and remain our flagship model.
Wodan — this model is an entirely experimental project with an all-wood earcup. We tested our new wood processing technology, tinkered with the earcup depth a little, and tried new cushioning materials. It turned out pretty interesting as a result: Wodan deliver a relatively smooth sound with a gently raised bass and lower section of the mid-frequency range, but with a focus on highlighting the maximum of details from any recording.
Odin (2019) is a model for those who liked the sound of original Odin, released back in 2015. In terms of sound, we tried to make this update as close to the original as possible, but with an updated driver and with a new headband. Generally speaking, Odin 2019 is for metalheads, especially when combined with earpads with small diameter perforations.
Q: These were current planar models. Are there any plans to expand the line?
K: Not at the moment. Moreover, we’re planning to discontinue Thror. For us, the top priority models are Thekk and Wodan. Even though the Thror deliver smoother sound, they’re significantly more expensive to manufacture, for example, due to their tricky patented headband. People liked the new self-adjusting headband very much despite the fact that its design is actually very simple. So, the model’s gone less brutal and aesthetical, but in return — it sports a lot more comfortable design. It’s also worth noting that Thror are less popular: people rarely buy them, while Thekk are in huge demand. We just can’t manufacture Thekk fast enough to fulfill the demand.
Q: Will you please tell me about the planar drivers used — is there the one and the same driver for all models, or are there multiple different types?
K: The same carbon-based driver is used in Thekk and Thror. Thridi, Odin (2019) and Wodan sport the other: a steel-based driver.
Q: What do you mean by saying ‘based’?
K: The driver is made of several layers. It’s sort of a sandwich: there’s a grid, multiple CEM rings, a layer of film, a special layer of honeycomb structure material and a base ring.
The grid and the base ring can be made of carbon or steel. The difference in weight of these drivers is about 50 grams per driver — the carbon one is obviously lighter. That is, no less than 100 grams of weight difference per pair of headphones. Thanks to the technology used, Thekk turned out to be one of the lightest open-back planar headphones with this size of drivers. They’re not the lightest though, but one of them; they only weigh 390 grams.
Those drivers are, by the way, manufactured in Russia, from first to last step.
Q: Those ribbons in the middle are, if I get it right, the conductive paths. And why is there a layer with honeycomb structure?
K: This is the layer that prevents the film from stretching and evenly distributes the load over the entire membrane area. With this layer, the membrane won’t change its properties over time.
Q: Speaking of the manufacturing country, are all the components Russian-sourced?
K: As for the planar drivers, everything in here is manufactured in Russia. The only exception is magnets, which are produced to order in China, but are magnetized here in Saint Petersburg. The speakers are our own development but manufactured to order in Taiwan. The headband is made in Russia, and the earcups timber is supplied from different countries, including Russia, USA, Japan and a whole lot of other places. For the earpads, we most often use the Italian leather. As for the cables, they’re assembled to order by JIB company.
Q: Awesome! The planars situation makes more sense now. Now let’s move on to dynamic models.
K: Kennerton Vali. Vali are our subflagship. The open-back dynamic headphones deliver ‘warmer’, thicker and stronger sound, with a fairly smooth frequency response. They don’t require any powerful amplification, and can be used even with most smartphones. But, of course, they need a good setup to give it their all and reproduce any recording much better.
There’s a quite interesting story behind those. The first version of Vali had a special feature — their earpads. The engineer who designed the headphones insisted on a strictly defined internal volume of the earpads, a strictly defined depth and a strictly defined number of perforation holes. Like, exactly 467 and a half, a quarter of a hole more — and you’re dead. That’s what he thought is the only way to get the right sound. It was a very long and expensive technology to follow though, so they were only used for this model. Moreover, we’ve been receiving complaints from users about the earcups being too small, that their ears don’t fit in completely, and we couldn’t change anything.
Well, in the end, we decided to recalculate the Vali and equip them with our standard earpads, like in Thekk and Wodan, and the earcups of the same standard diameter, while preserving all the sound features. We ended up with a slightly different, more V-shaped sound — maybe less technically perfect, but more ‘tasty’. And we liked the result. After all, there’s a lot of other analytically sounding models on the market, but it’s a rare case when the sound is ‘tasty’, detailed and not too crooked in terms of measurements.
Magni are closed-back headphones based on a graphene membrane emitter with a triple magnetic system. The first version was technically imperfect: there was a resonant peak within upper frequencies range because of the poorly cushioned back wall in some pieces. So we started to improve the design. For instance, we’ve got correct cushioning by the wooden frame and gave the holed metal flange some cushioning, too.
As for the overall tuning, Magni are pretty bass-focused (judging by figures), but subjectively even-sounding headphones. They provide a fantastic sound stage, but need to be warmed up, they just won’t sound as good as they can without it.
Q: I’ve noticed that you like to modify your models little by little. Why is it so?
K: Because we want to provide high-quality products with non-fading features, and we’re constantly improving our production culture. For example, we used to have an average measurement discrepancy between the left and the right speaker of 1-2 dB. Just like every other manufacturer, right? But now we only have such discrepancy within some frequencies, if any. And when the discrepancy is even here, it’s only about 0.5 dB.
We actually modify some aspects without people even noticing it. We optimize the designs to speed up the assembly process, reduce the number of defects and further stabilize the headphones features. For example, the Magni currently on the market are actually the third version, although their appearance hasn’t changed a bit. The speaker is now mounted in a unistructural earcup with thick walls to avoid resonance. We don’t use plastic (nor any other materials that would clink at different frequencies) for internal parts anymore. And, as I’ve already said, we’ve introduced correct cushioning thanks to a new metal part of the back cover.
The second story about Magni: at some point, it turned out that the speaker we use is able to play sound at a power of 1.5 W — just like a small bookshelf speaker. What’s even more surprising, there were people who listened to these headphones that loudly. Under such conditions, the emitter has a swing of 5 mm forward, while our earcups are only built for 2 mm swing. That is, the driver’s membrane dashed against the protective grid. We fixed this — the driver is now recessed deeper into the housing, and the protective grid is more curvy so that the driver doesn’t even touch it in any usage scenario.
Through continuous design optimization, we achieved a very simple structure, that’s why these headphones are now easy to modify, disassemble and assemble without ruining the whole thing. Of course, as a manufacturer, we can’t recommend to do so, but, to be honest with you and myself, you can easily change the cushioning, make the earcups more open-back or closed-back, and so on.
Q: But it’s very easy to damage the driver by playing an engineer. How often do you have to repair broken headphones?
K: It happens, but mostly it’s about incorrect usage and handling. It’s a pretty frequent case, when someone puts newly bought headphones on their head, the fit didn’t seem very comfortable to them from first try, and they sharply press, almost slam the earcups against their ears. The pressure drop may make the speakers go kaput, so you don’t want to ever do this. Not only dynamic headphones may be broken after this, but planar ones, too. At an exhibition, we once saw the Abyss headphones gone the similar way. For some reason, a person just slammed the membranes with their palms. Even fairly dense graphene membranes can’t endure it.
So we started providing instructions on how NOT to handle headphones. For example, don’t plug them into an outlet, don’t push them with your hands, don’t use them as speakers with a powerful amplifier, and so on.
Q: Does your 2-year warranty apply to all models?
K: Yes, a 3-year warranty applies to all 9 full-sized headphones models.
Q: We got off the dynamic models… How about we get back to the subject?
K: Well, yes. The next one is M12s (2020).
The M12s (2020) evolved from a semi-open model developed to order for a certain media company. The sub-bass was almost non-existent in them, since they were intended for professional studio recording purposes. The whole product was very light, with a non-replaceable twisted cable up to 3.5 meters long, velour earpads — they had basically everything you need to comfortably work for a long time.
To adapt this model for the market, we changed the headband finish to a metal hybrid one, so the headband stopped ringing when you unintentionally touch or hit it while using the headphones. We choose a different cushioning material and made these headphones a completely closed-back model.
That’s how we’ve got our M12s (2020) — headphones similar in sound to the Magni, only with a slightly darker hint. It’s now pretty difficult to compete with these within the corresponding price range.
And the last, but not least: Gjallarhorn — our closed-back horn-type headphones. As a general rule, horns are used to increase the sound pressure. We’ve been experimenting with horns for a long time and tried, for example, oval horns. There was even an option without earpads at all. We adopted the speaker from Magni, but due to their horn-type design, Gjallarhorn sound louder at the same amplification, and a small, typical of Magni small peak at the top is shifted slightly higher up the frequency range. So we ended up with headphones delivering a very powerful sound pressure and an extremely accurate sound stage. We’re even planning on converting the Gjallarhorn to gaming headphones, just because they sport excellent positioning, excellent localization of all sounds.
By the way, Gjallarhorn and M12s (2020) don’t use XLR, but 3.5 mm jacks, just because the earcups aren’t that thick.
Q: I’m very curious about one aspect of horn-type headphones usage. Horns need some very precise manufacturing technique. Especially if talking about portable headphones, not large stadium systems. Roughly speaking, you have your earcups carved from wood using a CNC machine, and then somebody with a piece of sandpaper finishes the detail by hand. Is it still possible to deliver stable quality? And if so, is there a secret?
K: You’re right about the technology, and no, there are no secrets here. That’s exactly what our manufacturing culture is. You just need some practice, and after 50 earcups finished, the quality will stick to the same high level.
Q: OK, forget about the earcups. What about the earpads?
K: They pretty much affect the sound.
Q: That’s common sense, but how exactly? There are earpads with narrow or wide perforation holes…
K: A narrow perforation amplifies the sub-bass by 3 dB and raises the mid-frequencies range by the same 3 dB. The result is a thicker, more massive sound. For example, in case of the Thekk, this would be a rather significant individual modification. Therefore, this kind of earpads are a non-standard option in comparison to ‘bundled’ ones.
Q: So, if I choose the earpads with no perforation at all, the sound will be even more bass-saturated?
K: No, it doesn’t work this way. Given the features of our planar drivers, non-perforated earpads won’t get you any good sound at all. Perforation allows the air to reach the emitter from both sides. In our driver, we use a 2-side magnetic system, so it’s important to allow the air to inflow from both sides at a certain angle. Imagine a through perforation (for example, as the HiFiMAN have in some of their models): the driver just won’t work correctly. Depending on the holes diameter, you can get either too much of a bass, or no bass at all. But if you don’t opt for perforation at all, the membrane may even stall at a certain volume and frequency.
We don’t publish this information — on purpose. We prefer to have people contact us directly so that we can recommend something specific based on the materials, perforations, earpads thickness and so on. In other words, it’s always better when a person first tells us about any specific differences from the standard sound they expect, because then we’re able to give them some tips. Moreover, we don’t always have everything in stock — especially now that the earpads materials supply is interrupted due to the borders being sealed.
Well, we’ve been experimenting for a long time and decided on our regular version. I’d also mention that people often buy our standard earpads to use with ZMF, Audeze and other similar headphones. Because, you know, the earcup sizes are the same.
Q: Does the earcup wood kind affect the sound?
K: It does — in case of closed-back models, and mostly doesn’t in open-back ones. So it’s generally a matter of an individual aesthetic choice. For example, many people choose headphones to match their furniture color.
Q: I thought people buy headphones to listen to the music and not to decorate their rooms…
K: Well, if the choice is available, then why not?
Q: Tell me about your plans, if it’s possible. What can we, audiophiles, expect from Kennerton in the foreseeable future, other than the aforementioned Gjallarhorn-based gaming headphones?
K: Well, for example, we are currently working on new in-ear models.
Q: How about new DACs or amplifiers? Because as of now, you only offer Atlas.
K: We are working on this, too. The prototypes are already available, and not just Atlas-ish options. And not only desktop ones. For example, imagine a portable DAC+amplifier. A multi-bit one. With Bluetooth input support. How do you like it?
Q: Wow!
K: We also think that it would be cool if there was a desktop amplifier with a docking station for such a portable model… In other words, we’re working out the new concepts and experimenting.
We also consider developing a wireless full-size model with AptX HD and Bluetooth support.
Like this post? You can support me on patreon.